What is Porosity in Welding: Usual Sources and Reliable Treatments
What is Porosity in Welding: Usual Sources and Reliable Treatments
Blog Article
The Science Behind Porosity: A Comprehensive Overview for Welders and Fabricators
Comprehending the elaborate devices behind porosity in welding is essential for welders and makers making every effort for remarkable workmanship. As metalworkers dig into the depths of this sensation, they discover a globe governed by different elements that influence the formation of these minuscule spaces within welds. From the structure of the base products to the intricacies of the welding process itself, a wide variety of variables conspire to either aggravate or ease the visibility of porosity. In this detailed overview, we will certainly decipher the scientific research behind porosity, discovering its results on weld quality and unveiling advanced methods for its control. Join us on this trip through the microcosm of welding blemishes, where accuracy satisfies understanding in the quest of flawless welds.
Comprehending Porosity in Welding
FIRST SENTENCE:
Assessment of porosity in welding reveals crucial understandings into the honesty and top quality of the weld joint. Porosity, identified by the presence of cavities or spaces within the weld steel, is a common issue in welding processes. These gaps, otherwise correctly addressed, can compromise the architectural honesty and mechanical buildings of the weld, resulting in potential failures in the completed item.
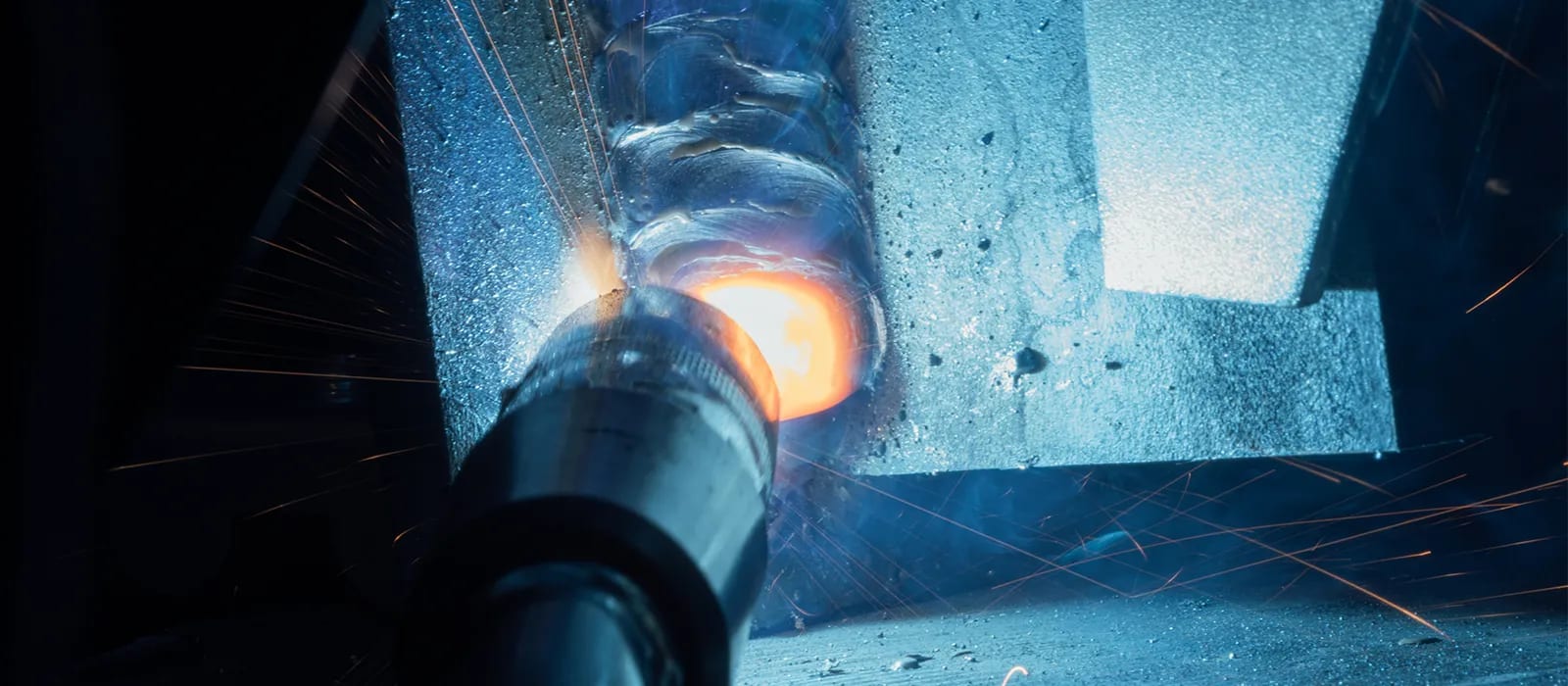
To discover and measure porosity, non-destructive screening approaches such as ultrasonic testing or X-ray examination are often utilized. These strategies allow for the recognition of internal flaws without endangering the stability of the weld. By analyzing the dimension, shape, and circulation of porosity within a weld, welders can make educated choices to enhance their welding procedures and attain sounder weld joints.

Factors Influencing Porosity Formation
The event of porosity in welding is affected by a myriad of aspects, ranging from gas securing efficiency to the complexities of welding parameter settings. One crucial variable adding to porosity formation is poor gas securing. When the protecting gas, normally argon or carbon dioxide, is not successfully covering the weld swimming pool, climatic gases like oxygen and nitrogen can infect the liquified metal, resulting in porosity. In addition, the tidiness of the base materials plays a considerable function. Pollutants such as corrosion, oil, or dampness can evaporate during welding, producing gas pockets within the weld. Welding criteria, including voltage, existing, travel rate, and electrode kind, likewise impact porosity development. Utilizing incorrect setups can create too much spatter or heat input, which subsequently can cause porosity. In addition, the welding method utilized, such as gas metal arc welding (GMAW) or protected metal arc welding (SMAW), can influence porosity formation due to variants in warmth distribution and gas coverage. Recognizing and managing these look at these guys aspects are vital for decreasing porosity in welding procedures.
Results of Porosity on Weld Top Quality
Porosity formation dramatically compromises the structural stability and mechanical residential or commercial properties of welded joints. When porosity exists in a weld, it develops voids or dental caries within the product, lowering the general stamina of read this post here the joint. These voids serve as anxiety concentration factors, making the weld a lot more at risk to splitting and failure under load. The existence of porosity additionally deteriorates the weld's resistance to rust, as the trapped air or gases within deep spaces can respond with the surrounding environment, causing deterioration with time. In addition, porosity can impede the weld's capacity to hold up against pressure or impact, additional endangering the total quality and dependability of the welded framework. In critical applications such as aerospace, automotive, or architectural building and constructions, where safety and sturdiness are critical, the destructive impacts of porosity on weld high quality can have extreme effects, emphasizing the importance of lessening porosity via proper welding strategies and treatments.
Strategies to Lessen Porosity
Furthermore, using the proper welding criteria, such as the right voltage, current, and travel rate, is critical in preventing porosity. Keeping a consistent arc length and angle during welding also assists minimize the probability of porosity.

Making use of the proper welding method, such as back-stepping or employing a weaving activity, can also aid distribute heat evenly and reduce the opportunities of porosity formation. By implementing these strategies, welders can efficiently minimize porosity and generate top notch welded joints.
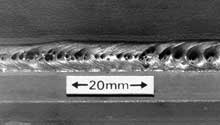
Advanced Solutions for Porosity Control
Executing innovative technologies and ingenious approaches plays a pivotal duty in accomplishing premium control over porosity in welding processes. next page Furthermore, using advanced welding methods such as pulsed MIG welding or changed atmosphere welding can also aid reduce porosity concerns.
An additional advanced service includes using advanced welding equipment. Using devices with built-in functions like waveform control and innovative power resources can boost weld top quality and lower porosity risks. The implementation of automated welding systems with precise control over criteria can considerably lessen porosity problems.
Moreover, incorporating innovative surveillance and evaluation innovations such as real-time X-ray imaging or automated ultrasonic testing can help in discovering porosity early in the welding process, allowing for instant restorative actions. In general, integrating these innovative remedies can substantially enhance porosity control and improve the overall top quality of bonded parts.
Verdict
In final thought, recognizing the science behind porosity in welding is essential for welders and producers to create top quality welds - What is Porosity. Advanced remedies for porosity control can even more boost the welding process and make sure a solid and reputable weld.
Report this page