Comprehensive Guide: What is Porosity in Welding and Just How to avoid It
Comprehensive Guide: What is Porosity in Welding and Just How to avoid It
Blog Article
Porosity in Welding: Identifying Common Issues and Implementing Ideal Practices for Prevention
Porosity in welding is a prevalent issue that usually goes unnoticed till it causes considerable troubles with the stability of welds. In this conversation, we will explore the key aspects contributing to porosity formation, analyze its detrimental impacts on weld efficiency, and talk about the finest practices that can be taken on to reduce porosity event in welding processes.
Typical Reasons For Porosity
One more regular perpetrator behind porosity is the visibility of impurities externally of the base steel, such as oil, oil, or rust. When these contaminants are not efficiently eliminated prior to welding, they can evaporate and come to be entraped in the weld, creating flaws. In addition, making use of filthy or wet filler materials can present impurities right into the weld, adding to porosity problems. To reduce these common reasons for porosity, detailed cleansing of base steels, proper shielding gas option, and adherence to ideal welding specifications are important techniques in accomplishing high-grade, porosity-free welds.
Influence of Porosity on Weld High Quality

The existence of porosity in welding can dramatically compromise the structural stability and mechanical properties of welded joints. Porosity produces gaps within the weld steel, weakening its general stamina and load-bearing ability.
Welds with high porosity levels often tend to show reduced effect stamina and minimized capability to warp plastically prior to fracturing. Porosity can hamper the weld's capacity to efficiently transfer forces, leading to premature weld failure and possible safety and security dangers in crucial structures.
Ideal Practices for Porosity Prevention
To improve the architectural integrity and quality of welded joints, what certain actions can be implemented to reduce the event of porosity during the welding procedure? Making use of the proper welding technique for the specific material being welded, such as changing the welding angle and weapon setting, can better protect against porosity. Regular inspection of welds and immediate remediation of any type of problems recognized throughout the welding procedure are crucial practices to prevent porosity and produce top quality welds.
Significance of Appropriate Welding Methods
Executing proper welding strategies is paramount in making certain the structural honesty and browse around here high quality of bonded joints, developing upon the structure of efficient porosity prevention procedures. Excessive warmth can lead to increased porosity due to the entrapment of gases in the weld pool. Additionally, utilizing the appropriate welding specifications, such as voltage, current, and travel speed, is vital for attaining sound welds with marginal porosity.
Additionally, the selection of welding process, whether it be MIG, see here now TIG, or stick welding, must align with the particular needs of the project to make sure optimum results. Appropriate cleaning and preparation of the base metal, along with selecting the ideal filler product, are also crucial elements of competent welding methods. By sticking to these ideal practices, welders can reduce the danger of porosity development and produce high-grade, structurally audio welds.
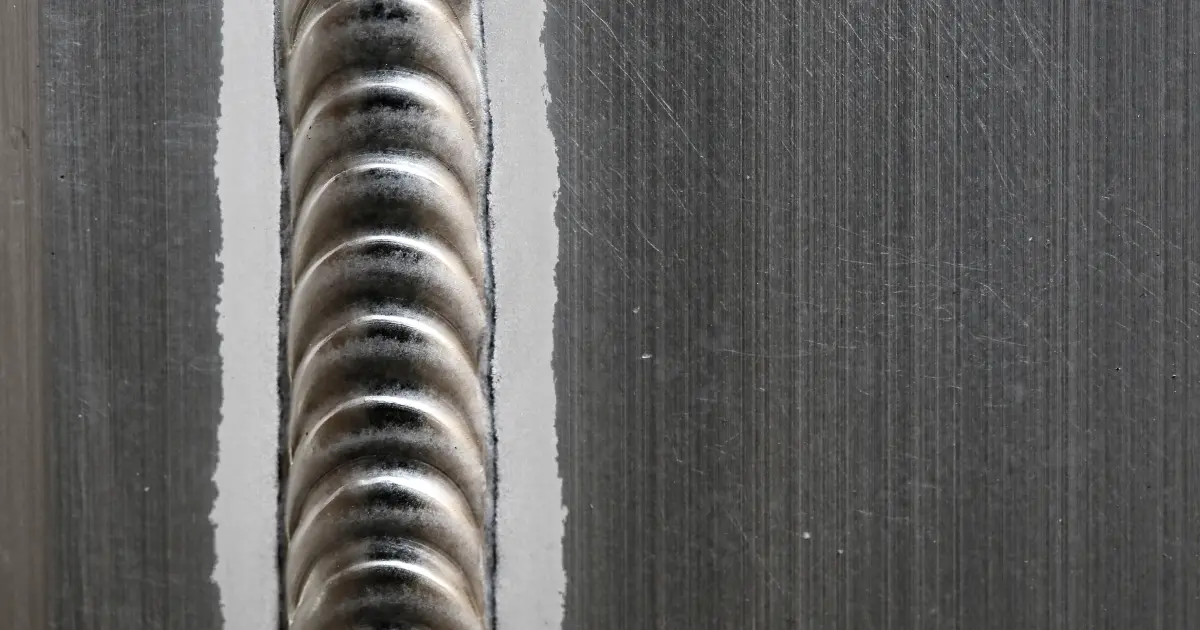
Checking and Quality Assurance Steps
Checking treatments are crucial to spot and prevent porosity in welding, making sure the stamina and resilience of the final product. Non-destructive testing methods such as ultrasonic screening, radiographic screening, and visual assessment are commonly employed to identify potential issues like porosity.
Post-weld assessments, on the various other hand, evaluate the last weld for any type of problems, including porosity, and validate that it meets specified criteria. Implementing a detailed top quality control plan that includes complete website link screening procedures and assessments is extremely important to reducing porosity problems and ensuring the total high quality of welded joints.
Final Thought
Finally, porosity in welding can be an usual problem that impacts the quality of welds. By determining the typical root causes of porosity and applying best practices for prevention, such as proper welding methods and testing procedures, welders can make certain premium quality and reliable welds. It is important to prioritize prevention techniques to reduce the incident of porosity and preserve the stability of welded structures.
Report this page